Decreased heat dissipation performance:
When the flatness of the bonding surface between the bottom of the IGBT package and the heat sink is poor, the contact area between the two will decrease, and the degree of contact tightness will also decrease. This will hinder heat transfer and reduce heat dissipation performance.
Poor heat dissipation can prevent the timely discharge of heat generated by IGBT during operation, resulting in an increase in internal temperature of the device. High temperature environments can accelerate the aging process of accelerator components, reducing their reliability and service life.
Increased thermal stress:
Due to poor flatness of the bonding surface, there may be gaps between the IGBT package and the heat sink. These gaps will generate thermal stress when the temperature changes, causing additional burden on the packaging structure.
Long term thermal stress may cause cracks, delamination, or deformation inside the packaging structure, which in turn can affect the electrical performance and reliability of the device.
2、 IGBT short-circuit failure mechanism
The short-circuit failure of IGBT is usually the result of multiple factors working together, including but not limited to:
Internal defects: such as process defects, material defects, etc. in the manufacturing process, which may cause device failure under thermal stress excitation.
External factors, such as overvoltage, overcurrent, electrostatic discharge, etc., may directly damage the internal structure of IGBT or cause its performance degradation.
Poor heat dissipation: Long term high temperature environment will accelerate the aging process of IGBT, reduce its ability to withstand current and voltage, thereby increasing the risk of short-circuit failure.
3、 Indirect correlation between flatness difference and short circuit failure
Although the poor flatness of the bonding surface between the bottom of the IGBT package and the heat sink will not directly cause IGBT short-circuit failure, it will increase the risk of short-circuit failure through indirect factors such as affecting heat dissipation performance and increasing thermal stress. Specifically:
Decreased heat dissipation performance leads to high temperature environment: As mentioned earlier, poor flatness of the bonding surface can cause a decrease in heat dissipation performance, resulting in IGBT being in a high temperature environment during operation. High temperature environments can accelerate the aging process of components, reduce their reliability and service life, and increase the risk of short-circuit failure.
Increased thermal stress leads to structural damage: Poor flatness of the bonding surface may also generate additional thermal stress, which can burden the packaging structure. Long term thermal stress may lead to problems such as cracks, delamination, or deformation inside the packaging structure. These structural damages may damage the internal electrical connections of IGBT or cause its performance degradation, thereby increasing the risk of short-circuit failure.
4、 Response measures
In order to reduce the impact of the flatness difference between the bottom of the IGBT package and the heat sink on the reliability and service life of the device, the following measures can be taken:
Improve the flatness of the bonding surface: During the packaging process, the production process and parameters should be strictly controlled to ensure that the flatness of the bonding surface between the bottom of the IGBT package and the heat sink meets the requirements.
Optimize heat dissipation design: Adopt more efficient heat dissipation structures and materials to improve heat dissipation efficiency and reduce the operating temperature of devices.
Strengthen thermal management: Conduct regular thermal management monitoring and maintenance of IGBT modules to promptly identify and address potential heat dissipation issues.
Improving device quality: Using high-quality raw materials and manufacturing processes to reduce internal defects and failure rates of devices.
In summary, there is a certain indirect correlation between the poor flatness of the bonding surface between the bottom of IGBT packaging and the heat sink and the short-circuit failure mechanism of IGBT. Therefore, in the manufacturing, use, and maintenance process of IGBT, the flatness of the bonding surface should be highly valued, and effective measures should be taken to solve it.
IGBT package bonding flatness test case: (Color temperature chart represents 3D high and low information, table shows measured deformation)
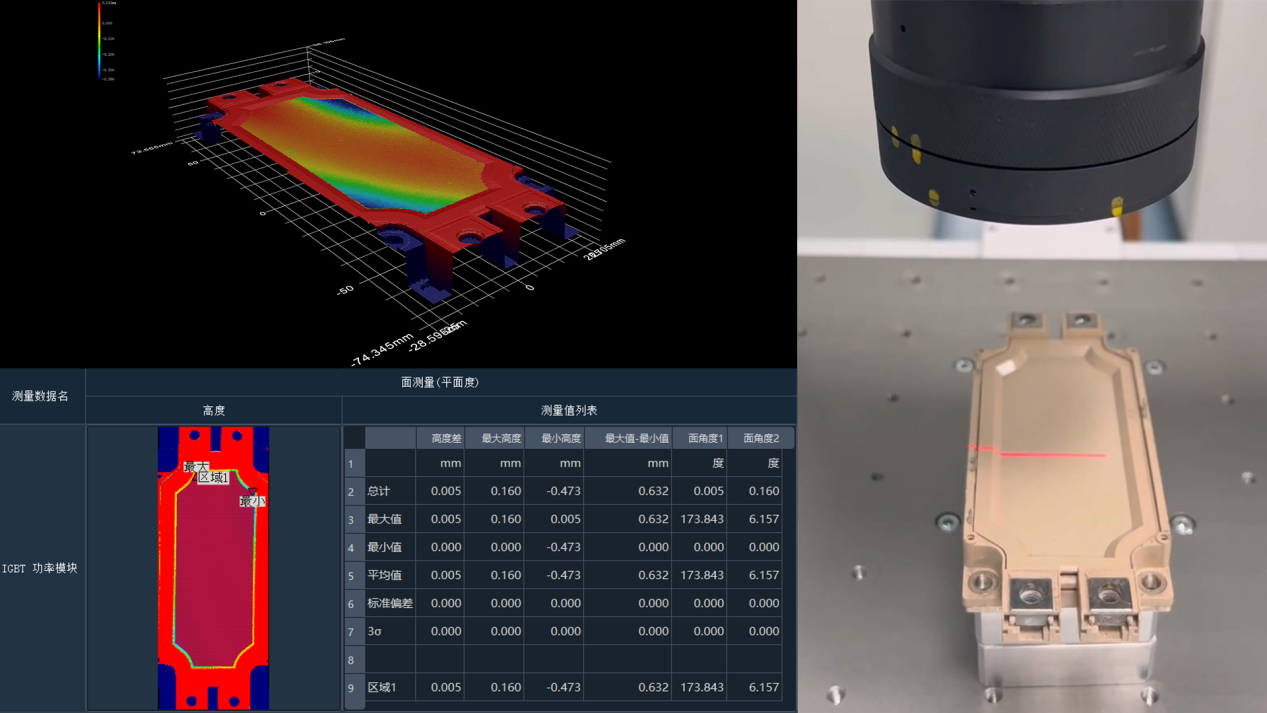
4、 Introduction to Laser Frequency Comb 3D Optical Contour Measurement System
The laser optical frequency comb 3D contour measurement system utilizes the principle of laser frequency comb and adopts high-frequency laser pulse flight distance measurement method, which is not afraid of traditional optical obstruction problems and fully applicable to the measurement of various complex large structural components, solving the difficulties of traditional optical measurement such as deep holes and grooves. The laser frequency of 500kHz has brought technological innovation to the automation of detection.
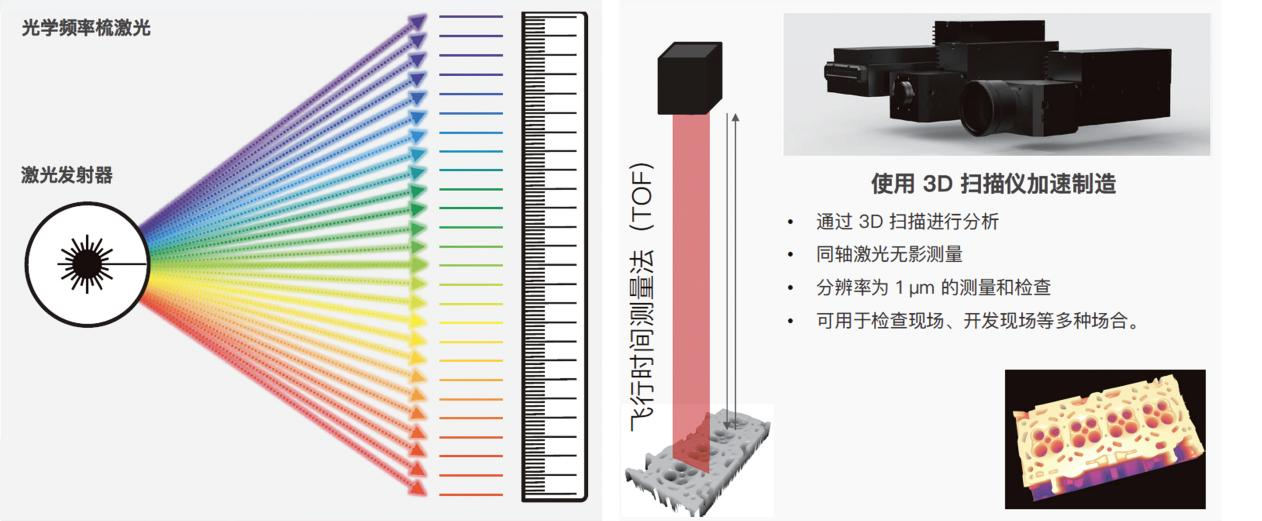
Technical feature one: coaxial shooting, flight ranging scanning method, not afraid of traditional optical "obstruction" problems.
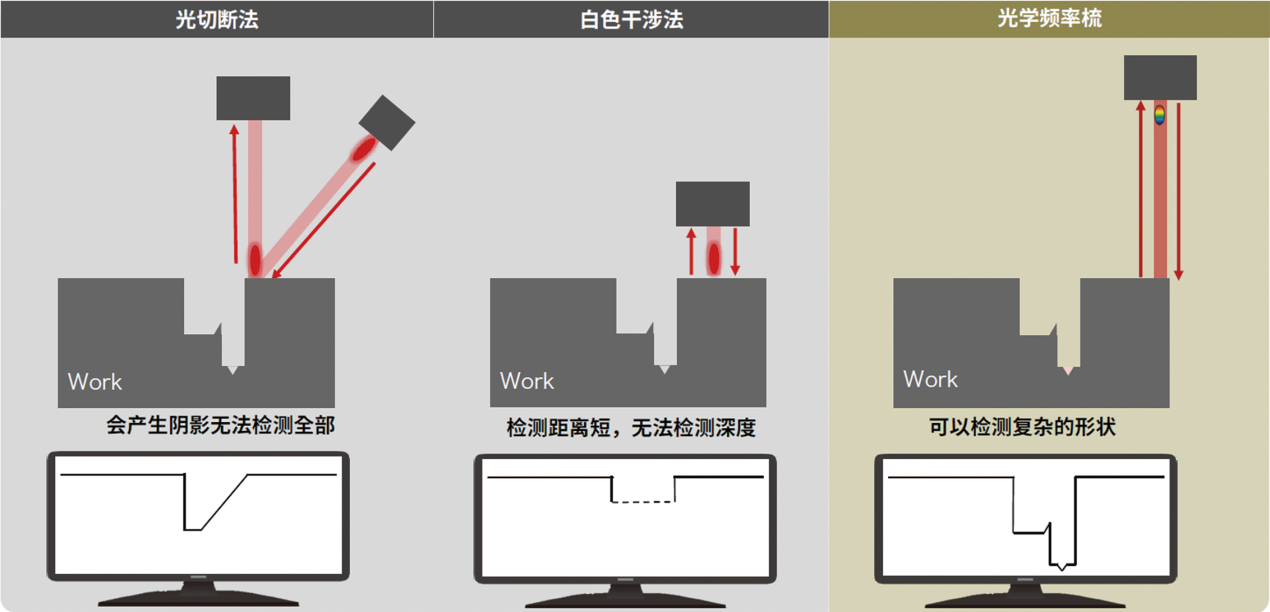
Actual case: Valve body oil circuit board with vertical and horizontal grooves
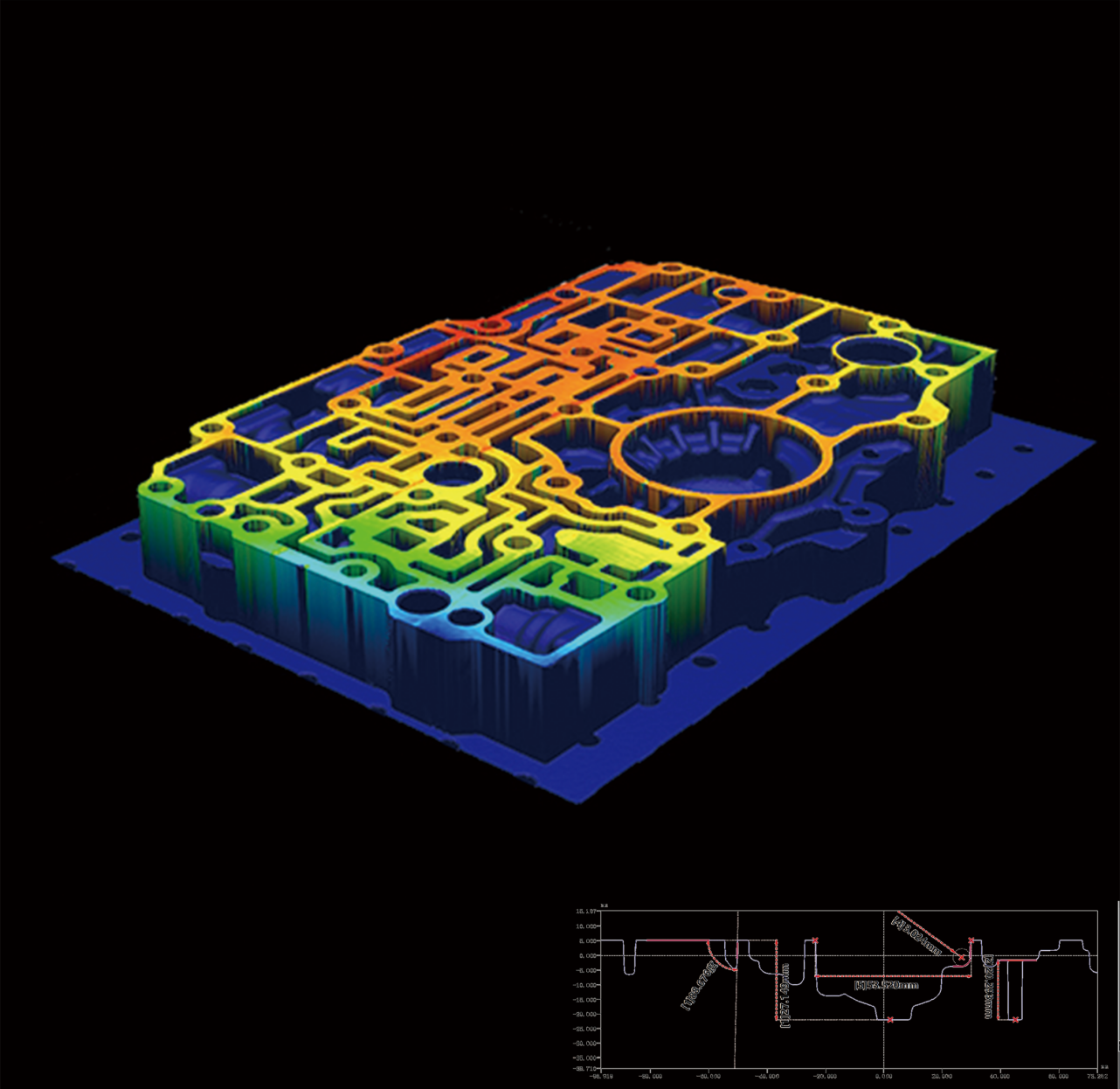
Technical feature 2: With an accuracy of ± 2um, it can achieve a maximum height/depth scanning imaging of 130mm
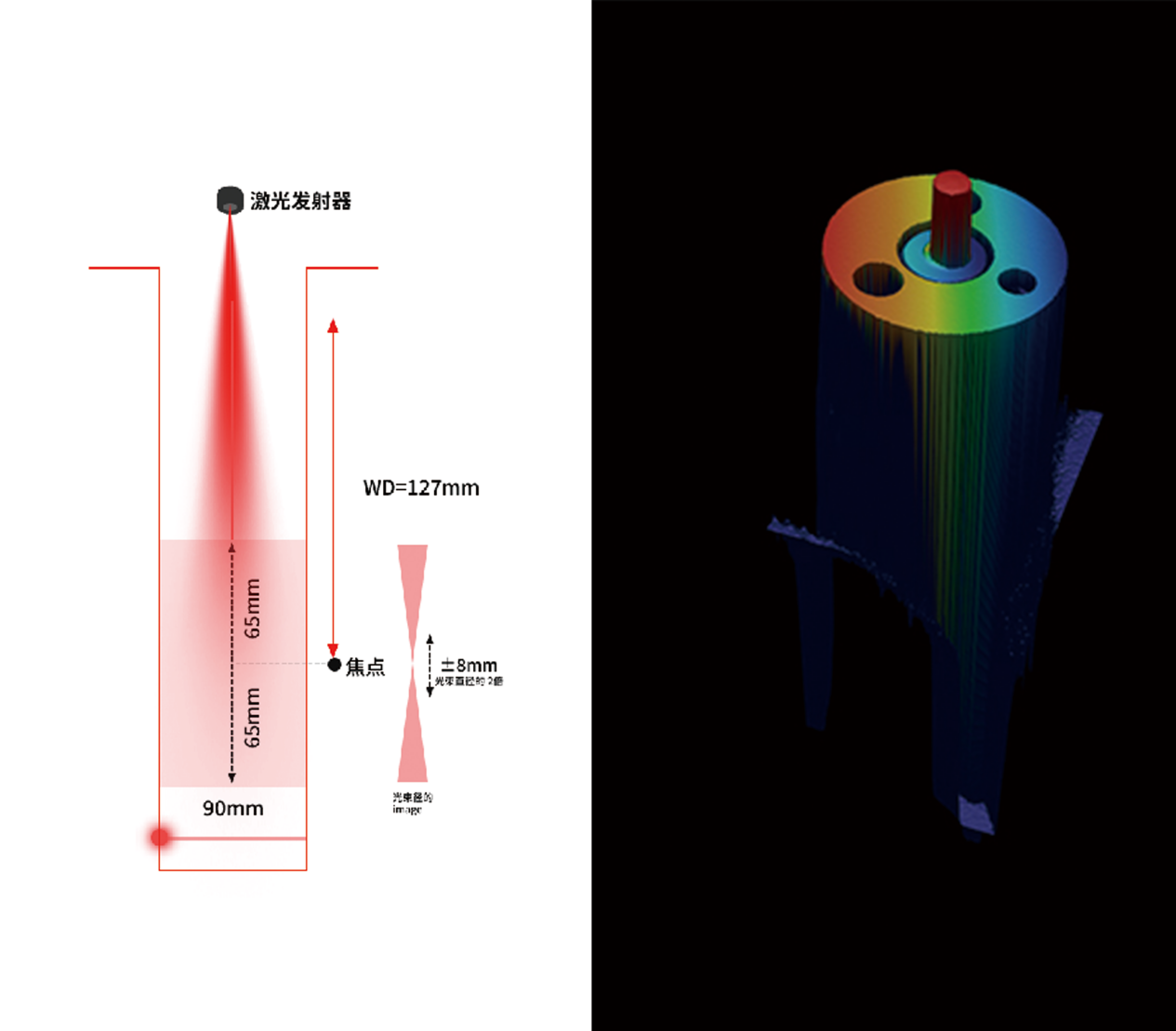
Technical feature three: It can be equipped with multiple lens combinations to achieve scanning with a large field of view of tens of meters.
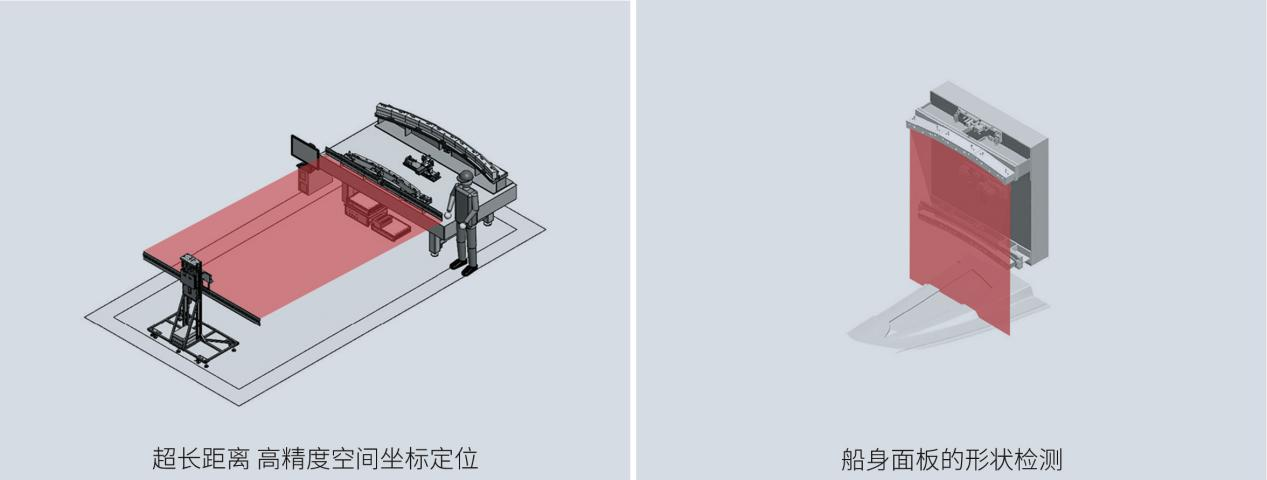
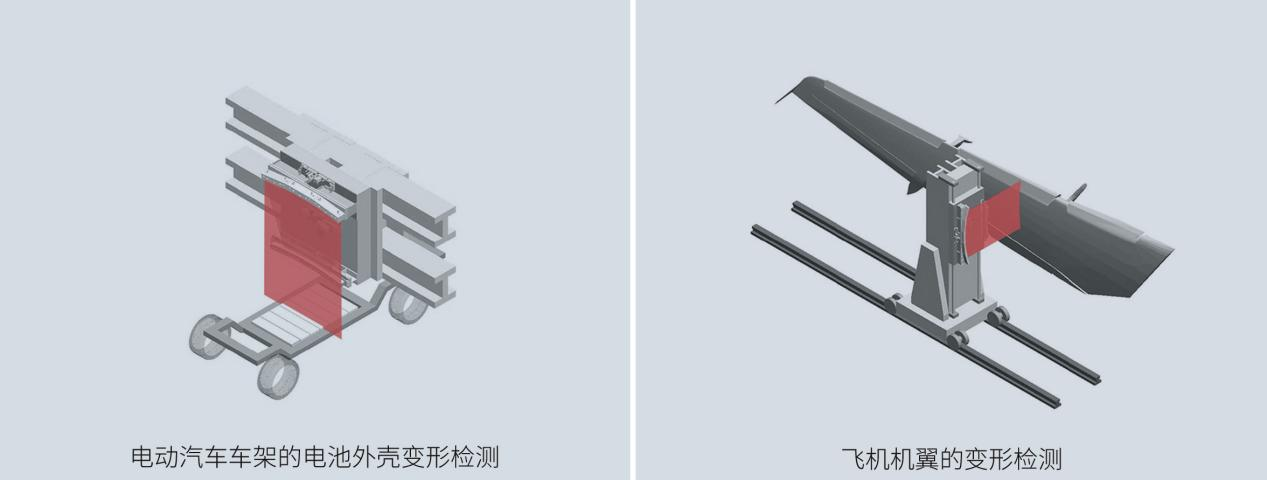