When the flatness of the bonding surface between the bottom of the IGBT package and the heat sink is poor, a series of adverse effects will occur:
Reduced contact area: Poor flatness of the bonding surface leads to a decrease in the contact area between the chip and the heat sink, narrowing the channel for heat transfer and affecting heat dissipation efficiency.
Increased contact thermal resistance: The decrease in contact area and the presence of gaps will increase the contact thermal resistance, hindering the transfer of heat from the chip to the heat sink, resulting in an increase in chip temperature.
Stress concentration: Due to uneven bonding surfaces, uneven areas of the chip are prone to stress concentration when subjected to temperature changes or external forces. Especially at the connection between the bonding wire and the chip, stress concentration may cause the bonding wire to experience additional mechanical stress.
2、 Reasons for Bond Brittle Fracture
Bond fracture is a common form of IGBT module failure, which is mainly caused by:
Material difference: There is a difference in the coefficient of thermal expansion between the bonding wire and the chip material. When the temperature changes, due to the different coefficients of thermal expansion, there will be relative displacement between the bonding wire and the chip, resulting in stress concentration.
Stress accumulation: Working in a stress concentrated environment for a long time, the bonding wire will gradually accumulate fatigue damage. When the damage reaches a certain level, the bonding wire will undergo brittle fracture.
Process defects: Defects in the packaging process, such as poor bonding wire connections, improper selection of packaging materials, etc., may also lead to brittle fracture of the bonding wire.
3、 Response measures
In order to reduce the impact of the flatness difference between the bottom of the IGBT package and the bonding surface of the heat sink on the bonding wire, the following measures can be taken:
Improve the flatness of the bonding surface: By improving the processing technology and quality control measures, the flatness of the bonding surface between the bottom of the IGBT package and the heat sink can be improved. This can reduce the occurrence of stress concentration and lower the risk of bond fracture.
Optimize heat dissipation design: Adopt more efficient heat dissipation design, such as increasing heat dissipation area, optimizing heat dissipation structure, etc., to improve heat dissipation efficiency. This helps to reduce chip temperature and minimize the impact of thermal stress on bonding wires.
Strengthen packaging process control: Strictly control packaging process parameters and quality requirements during the packaging process. Ensure that the connection between the bonding wire and the chip is firm and reliable, reducing bonding failure issues caused by improper packaging processes.
Selecting appropriate bonding wire materials: Choose bonding wire materials with higher elastic modulus and better heat resistance to improve their stress and fatigue resistance.
In summary, the poor flatness of the bonding surface between the bottom of the IGBT package and the heat sink is one of the important reasons for stress concentration and bond fracture at the connection between the bonding wire and the chip. In order to improve the reliability and performance stability of IGBT modules, it is necessary to strictly control the packaging process, optimize the heat dissipation design, and select suitable bonding wire materials.
IGBT package bonding flatness test case: (Color temperature chart represents 3D high and low information, table shows measured deformation)
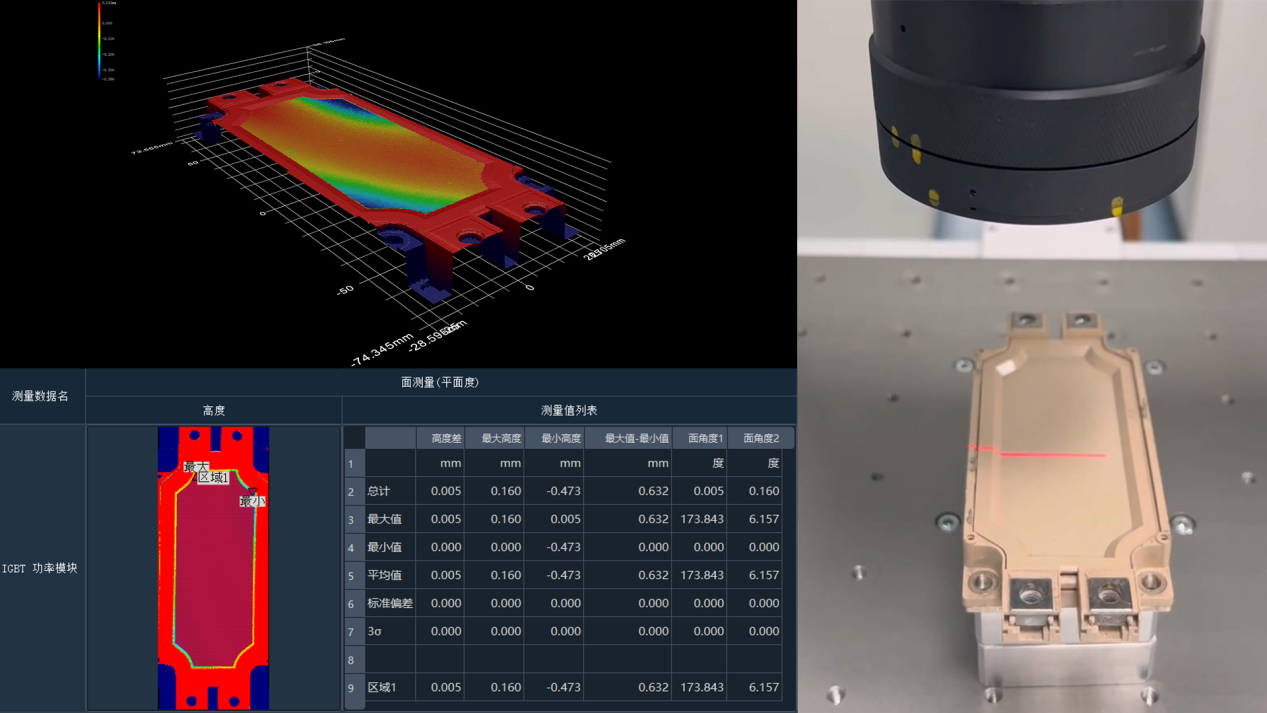
4、 Introduction to Laser Frequency Comb 3D Optical Contour Measurement System
The laser optical frequency comb 3D contour measurement system utilizes the principle of laser frequency comb and adopts high-frequency laser pulse flight distance measurement method, which is not afraid of traditional optical obstruction problems and fully applicable to the measurement of various complex large structural components, solving the difficulties of traditional optical measurement such as deep holes and grooves. The laser frequency of 500kHz has brought technological innovation to the automation of detection.
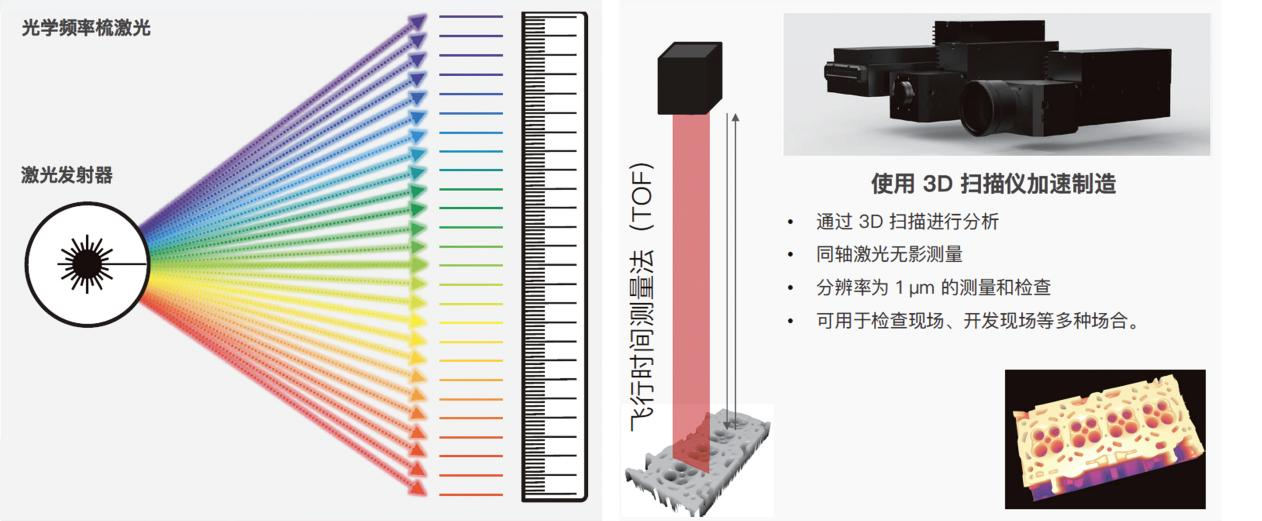
Technical feature one: coaxial shooting, flight ranging scanning method, not afraid of traditional optical "obstruction" problems.
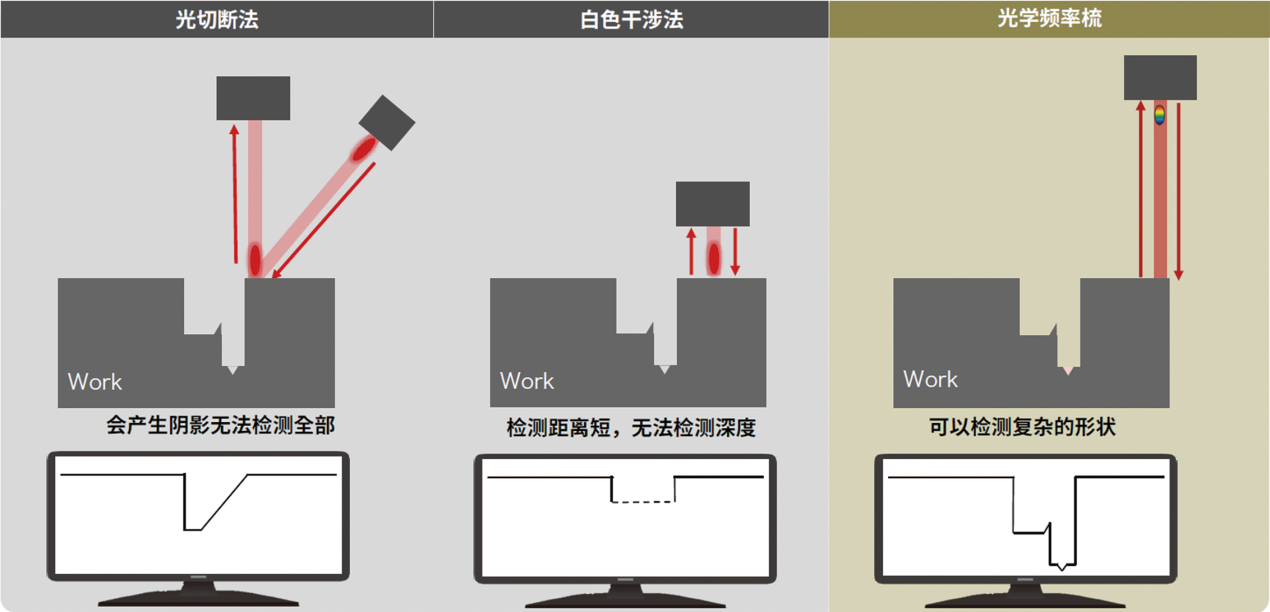
Actual case: Valve body oil circuit board with vertical and horizontal grooves
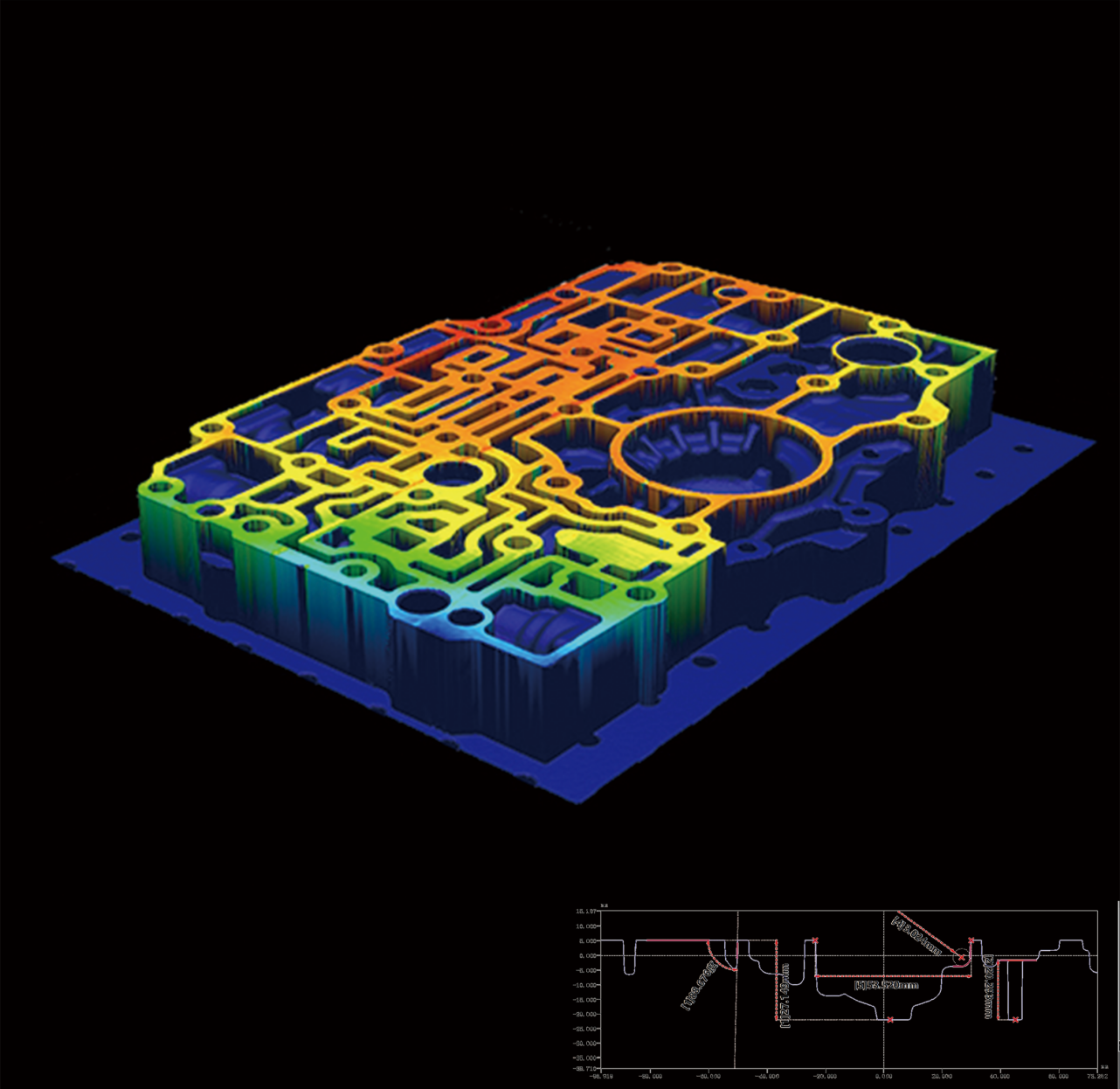
Technical feature 2: With an accuracy of ± 2um, it can achieve a maximum height/depth scanning imaging of 130mm
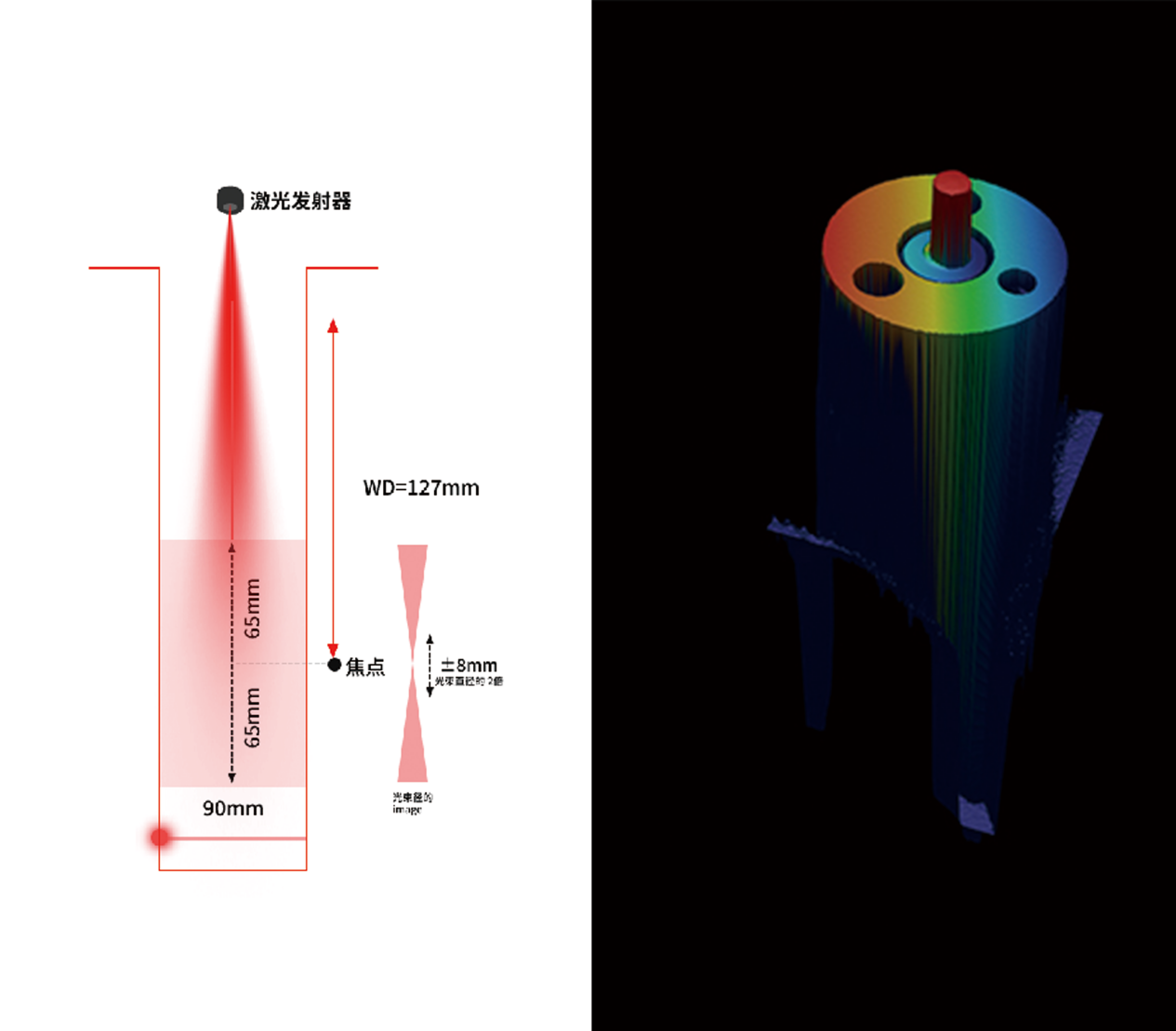
Technical feature three: It can be equipped with multiple lens combinations to achieve scanning with a large field of view of tens of meters.
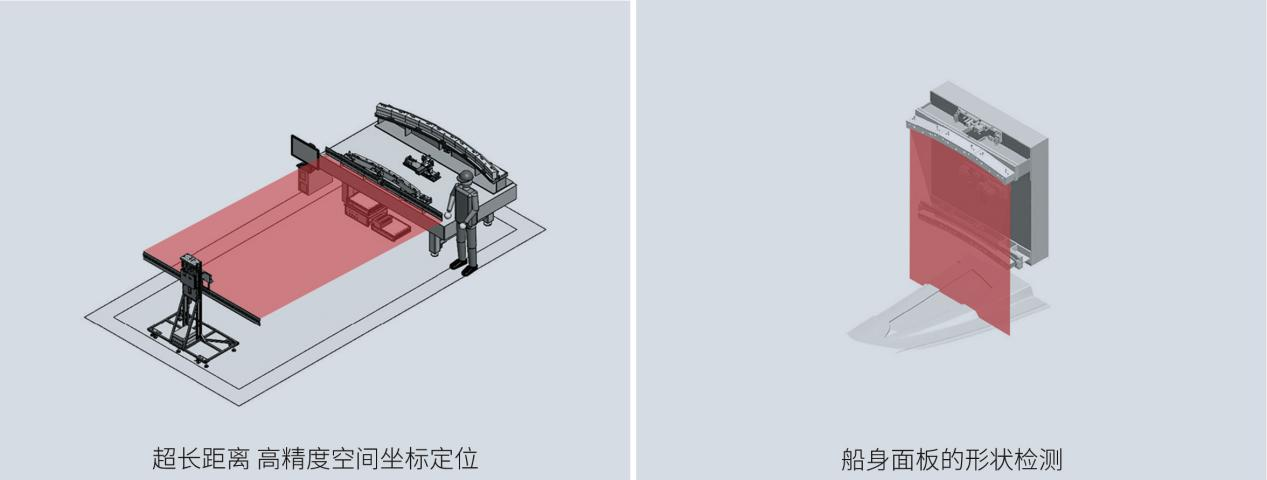
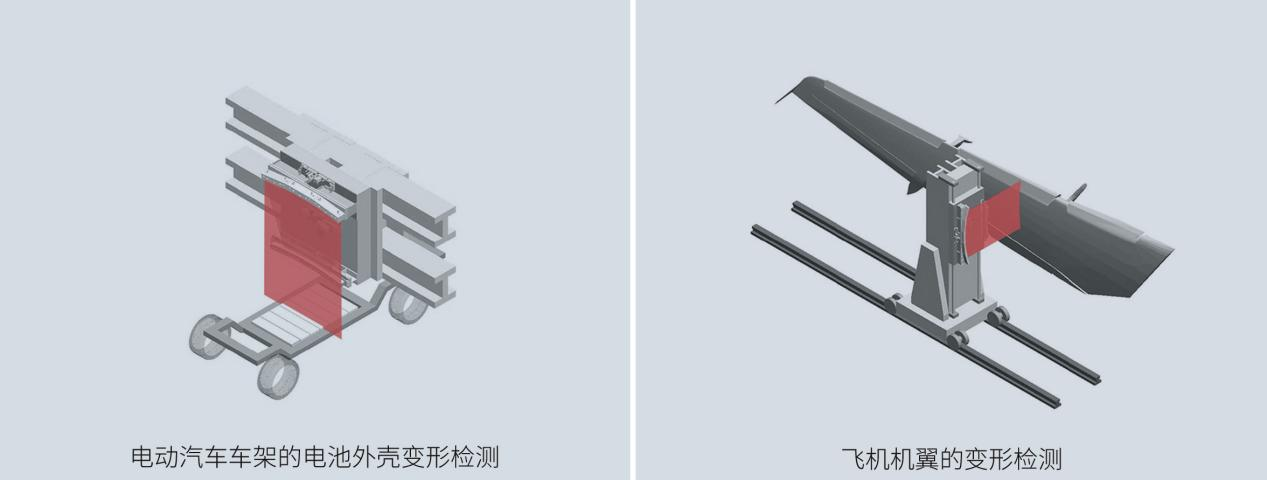