The morphology and dispersion medium of abrasives have a significant impact on the grinding quality of 4H silicon carbide (4H SiC) chips. The following is a detailed analysis of this impact:
1、 The influence of abrasive morphology
The morphology of abrasive is one of the key factors affecting the quality of 4H SiC chips during the grinding process. Diamond abrasive is a commonly used material for grinding 4H SiC chips due to its high hardness and wear resistance. The shape, size, and distribution of abrasives can affect the material removal rate and surface quality of chips during the grinding process.
Material removal rate: The shape and size of the abrasive directly affect its contact area and contact pressure with the surface of 4H SiC chips. Abrasives with sharp edges and larger sizes can more effectively penetrate the surface of the chip, thereby improving the material removal rate. However, excessively high material removal rates may lead to excessive scratches and damage on the surface of the chip.
Surface quality of chips: The morphology of abrasives can also affect the surface roughness and profile accuracy of chips. Irregular shaped or oversized abrasives may cause unevenness and scratches on the surface of the chip. On the contrary, abrasives with regular shapes and moderate sizes can produce more uniform material removal effects, resulting in better surface quality.
2、 The influence of dispersed media
The dispersing medium plays a role in uniformly dispersing the abrasive into the grinding solution and stabilizing its suspension during the grinding process. Common dispersion media include water-based systems and ethylene glycol systems.
Water based system: Water based grinding fluid has a high Zeta potential value, which helps to achieve uniform dispersion of abrasives. In addition, the high thermal conductivity of water is beneficial for controlling the surface temperature during the grinding process, preventing chip damage caused by excessive temperature. However, water-based grinding fluids may be affected by water quality and impurities, resulting in unstable grinding performance.
Ethylene glycol system: The Zeta potential jue of the ethylene glycol system grinding fluid is relatively small, and the abrasive is prone to agglomeration. This increases the penetration depth of the abrasive during the grinding process, resulting in an increased material removal rate of the chip. However, agglomerated abrasives may also cause deeper scratches and damage to the surface of the chip. In addition, the viscosity of the ethylene glycol system grinding fluid is relatively high, which may affect the fluidity and grinding efficiency of the grinding fluid.
3、 Overall consideration
In the actual grinding process, it is necessary to comprehensively consider the influence of abrasive morphology and dispersion medium to achieve good grinding results. Choosing the appropriate shape, size, and distribution of abrasives, as well as appropriate dispersion media and grinding fluid formulations, can optimize the material removal rate and chip surface quality during the grinding process. At the same time, it is necessary to adjust and optimize according to specific grinding processes and equipment conditions to achieve good grinding results and economy.
In summary, the morphology of abrasives and dispersion media have a significant impact on the grinding quality of 4H SiC chips. By optimizing the morphology of the abrasive and the selection of the dispersion medium, as well as setting the grinding process parameters, high-quality 4H SiC chips can be obtained.
4、 High throughput wafer thickness measurement system
The high-throughput wafer thickness measurement system, based on the principle of optical coherence tomography, can solve technical indicators such as wafer/chip thickness TTV (Total Thickness Variation), BOW (Bend), WARP (Warpage), TIR (Total Marked Reading), STIR (Site Total Marked Reading), LTV (Local Thickness Variation), etc.
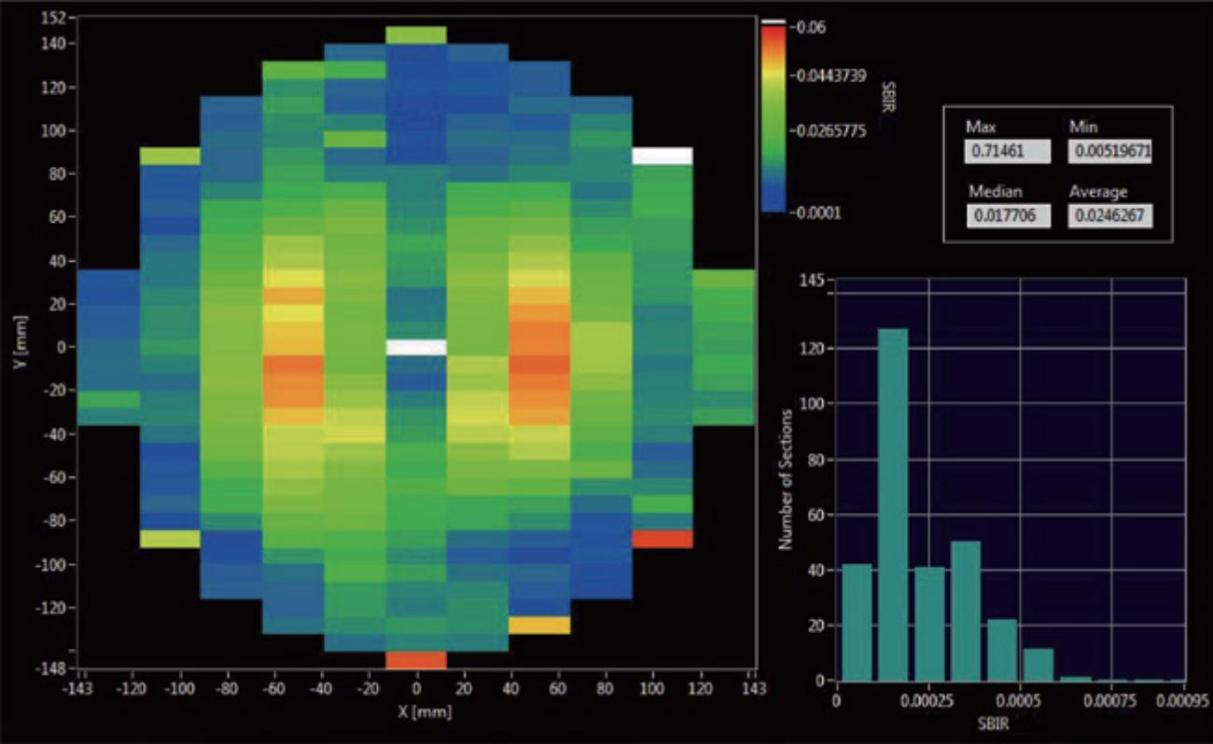
The high-throughput wafer thickness measurement system adopts the third-generation tunable scanning frequency laser technology, which is a traditional dual probe scanning method. It is compatible with 2-inch to 12 inch square and circular wafers, and can measure all flatness and thickness parameters at once.
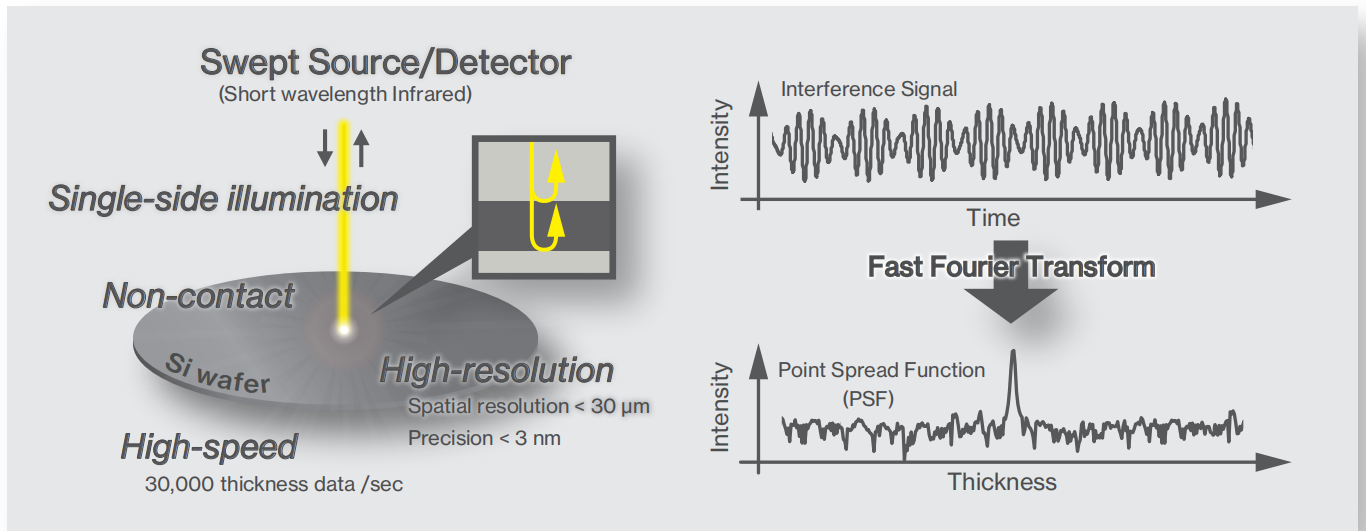
1. Flexible and applicable to more complex materials, from lightly doped to heavily doped P-type silicon (P++), silicon carbide, sapphire, glass, lithium niobate and other wafer materials.
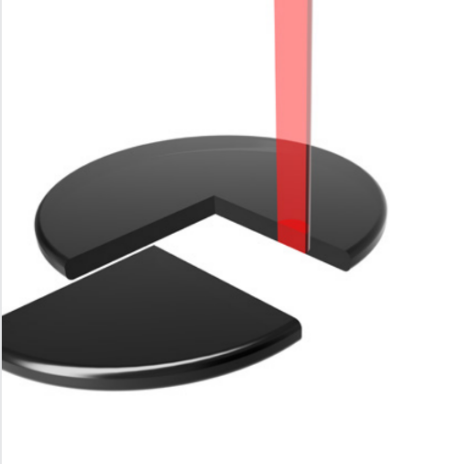
Heavy doped silicon (front and rear surface detection of strongly absorbing wafers)
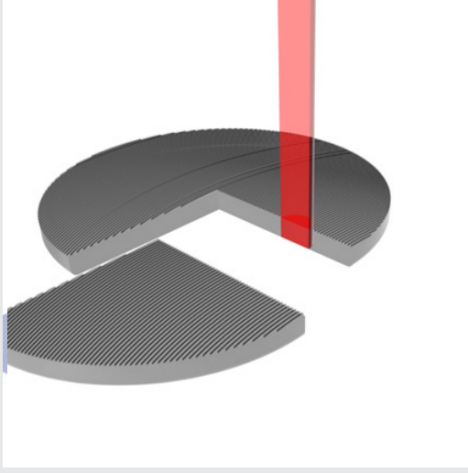
Rough wafer surface, (third-generation scanning frequency laser with point scanning, compared to spectral detection schemes, is less susceptible to interference noise from adjacent units in the spectrum, making it difficult to measure rough surface wafers)
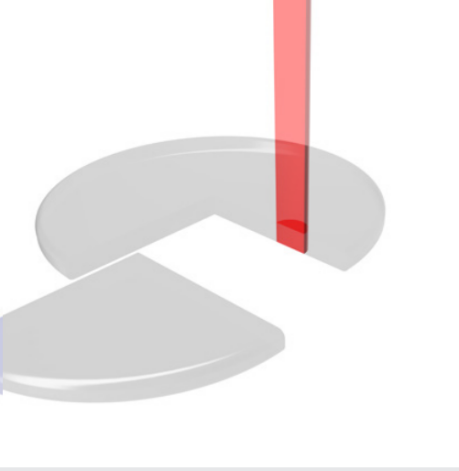
Low reflectivity silicon carbide (SiC) and lithium niobate (LiNbO3); (By compensating for polarization effects, enhance the signal-to-noise ratio of low reflection wafer surface measurements)
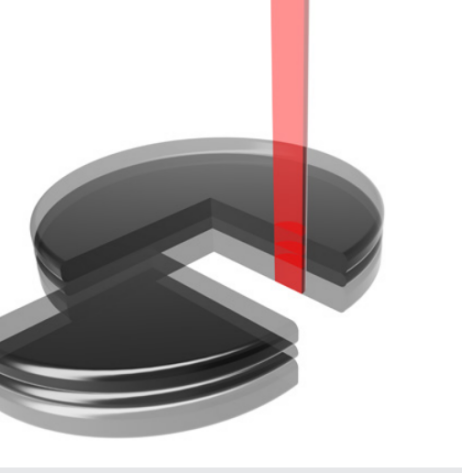
Silicon on insulator (SOI) and MEMS can simultaneously measure multi-layer structures, with thicknesses ranging from μ m to several hundred μ m.
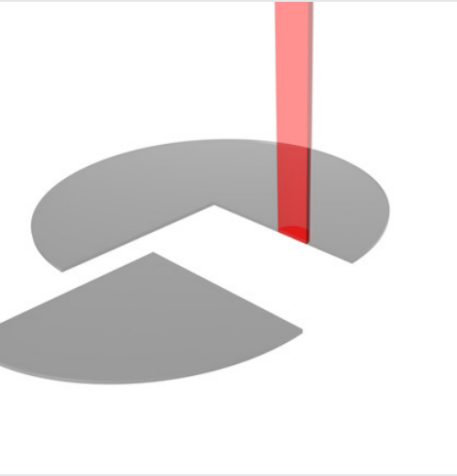
It can be used to measure the thickness of various thin films, with the thinnest thickness as low as 4 μ m and an accuracy of up to 1nm.
1. The "temperature drift" processing capability of tunable swept frequency lasers is reflected in their strong anti-interference ability in extreme working environments, which changes the heavy reliance on "active damping platforms" in traditional wafer measurement and significantly reduces costs.
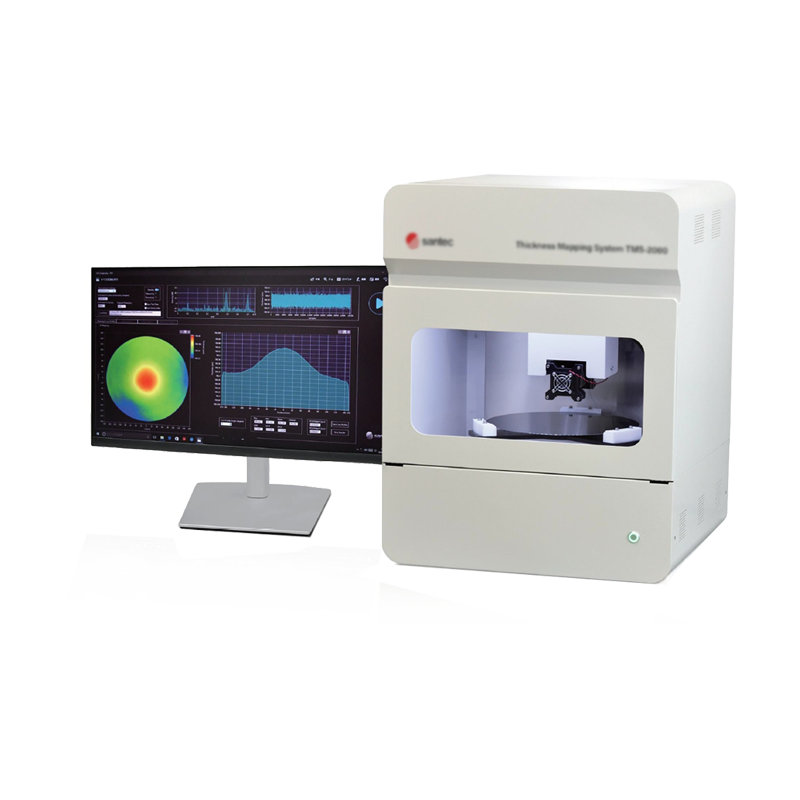
2. Flexible motion control method, compatible with measuring 2-inch to 12 inch square and circular pieces.